The impact of automation in manufacturing
This post was sponsored by AT&T Business, but the opinions are my own and don’t necessarily represent positions or strategies of AT&T Business.
Automation in manufacturing inspires humans and machines to work side by side. This automation is built on network modernization—the migration from outdated legacy and copper networks to today’s fiber internet networks. They deliver the bandwidth, speed, and lower latency so that everything from applications to cloud connectivity, robotics, and yes, automation can function with the efficiency they demand. This foundation is critical for manufacturing to have the flexibility to respond to market shifts and demands, as well as take advantage of the benefits of automation.
An excellent example of this was with the pandemic. As companies shifted to eCommerce models to meet consumer demand, distribution center network operations increased exponentially—by 28% totaling revenues of $36 billion. This growth was driven by warehouse automation. Companies like Amazon, which accounted for 35% of this growth, were big drivers of this increase.1 But this this didn’t happen in a vacuum of automation-only centers. These systems had to quickly integrate with humans to operate efficiently. As a result of the pandemic, we’re now living in an era of not only warehouse automation, but automation across industries. For example, retail and food services automation is a market that’s expected to surge by $34.23 billion by 2029.2
As new technologies such as robotics, artificial intelligence (AI), and machine learning (ML) continue to evolve, humans and machines are expected to increasingly work side by side in the manufacturing industry. The bridge to get there? Automation in manufacturing.
At its core, the term “automation” refers to the use of various technologies to streamline and optimize manufacturing processes. In this context, automation includes the use of robots, computer numerical control (CNC) machines, sensors, and other advanced technologies to enhance efficiency, productivity, and output.
The acceleration of automation in manufacturing—and the road ahead
Industry 5.0 is embracing AI. There’s no need for a scientific study to know that the acceleration of automation in manufacturing is a clear trend. The potential for how far we have to go is a startling wake-up call. Let’s look at the backstory behind why automation in manufacturing is accelerating.
- The increasing availability and affordability of advanced technologies, such as robotics, machine learning, AI, 5G, and the Internet of Things (IoT). These technologies have become more accessible to manufacturers of all sizes, allowing them to automate a wider range of tasks and processes than ever before.
- Rising labor costs. In many countries, the cost of labor has been increasing steadily, making it more expensive to hire and retain workers. As a result, manufacturers are turning to automation to reduce their reliance on human labor and save on costs in the long run.
- The need for greater speed and accuracy in production. Automated systems can perform tasks faster and more consistently than humans, which can help to reduce production times and increase output. In addition, automated systems can perform tasks with a high degree of accuracy and precision. Automation can help ensure quality control and minimize defects.
The acceleration of automation in manufacturing is expected to continue in the coming years, as manufacturers seek to improve efficiency, reduce costs, and increase productivity. However, it is important to recognize that automation can have significant implications for the workforce, and efforts should be made to ensure that workers are able to adapt and thrive in a changing manufacturing landscape.
5 Types of automation in manufacturing
As there are many type of manufacturing, there are several types of automation in manufacturing:
- Robotic automation: The use of robots to perform tasks such as welding, painting and assembly.
- Material handling automation: The use of conveyors, lifters, and other equipment to move materials and products through the manufacturing process.
- Inspection automation: The use of sensors and other technologies to inspect products for defects and quality control.
- Process automation: The use of software and other technologies to automate various aspects of the manufacturing process, such as scheduling, inventory management, and maintenance.
Individually or combined, these can bring better efficiency to manufacturing operations.
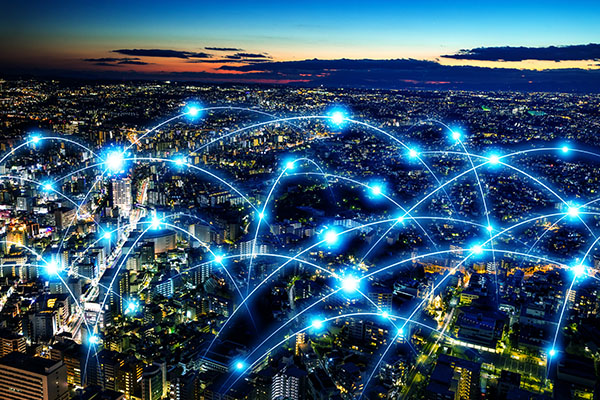
The ROI of network modernization
Network modernization can produce strong ROI for your business, but you need the right strategy and technology to exceed your digital transformation goals.
How are people employing automation today?
There are many ways that manufacturing operations can employ automation. However, several key use cases for automation in manufacturing stand out:
- Improve waste management: With video sensor technology, manufacturers can identify product abnormalities based on defined specifications and display real-time notifications. These alerts can then be charted on a dashboard to provide visibility into operations.
- Improve workforce safety: Intrusion detection as a feature of video intelligence can inform management when someone approaches the conveyor belt to help ensure safety standards are met.
- Reduce labor costs: By automating tasks that would otherwise require human labor, manufacturers can reduce their labor costs. Inventory tracking is a good example. With 5G and video intelligence, manufacturers can detect the number of boxes on a shelf and receive real-time notification when a box is removed. Management can receive alerts if someone places the box outside of the designated area too.
- Increase flexibility and agility: Network with built-in security can help manufactures respond quickly to changing market conditions and customer demand.
- Improve reliability: Reliable connectivity with backup connection ensures production is not disrupted.
Assessing Your automation maturity
Assessing your automation maturity is a critical step. This will help you to determine the effectiveness of your manufacturing processes and identifying areas where you can improve efficiency, productivity, and profitability. A few key considerations when evaluating your maturity:
- Start with your business goals when assessing your automation maturity. It is essential to understand how automation can help you achieve your goals, whether they are to reduce costs, increase production output, improve quality, or enhance customer satisfaction.
- Evaluate your network. Your network may seem to be functioning, but take a close look at if it can handle the demands of automation. If not, it’s time to modernize to a reliable fiber internet infrastructure.
- Benchmark the current state of automation including the technology and processes involved in your operations.
- Assess your current team expertise and identify capability and capacity gaps to achieve your goal.
- Assess your current manufacturing processes and identify areas that are manual, repetitive, or time-consuming and analyze how automation could be implemented to reduce or eliminate these tasks.
- Assess the technologies you currently use and identify areas where you can implement new or advanced technologies to improve your processes. This could include implementing reliable networks with embedded security, IoT and advanced wireless powered by 5G, robotics, and AI.
Assessing your automation maturity is a continuous process that requires ongoing monitoring and evaluation of your people, processes, and technology. By identifying areas for improvement and implementing new technologies, you can stay ahead of the curve and remain competitive.
Network, security, and building the smart factory
Smart factories—the connected factory—is the game changer for the U.S. manufacturing industry. Adoption of the technology is expected to result in threefold productivity improvements over the next decade. This is where network and security play a pivotal role. When identifying the right automation solution for your business, assess factors like:
- Cost: Consider the upfront cost of implementing the technology, ongoing maintenance or support fees, and the cost of training your staff to use the new technology.
- Security: Evaluate the reliability of the network connection and embedded security measures such as firewalls, access controls, encryption and backup connection to protect against potential cyber threats and ensure that sensitive data is kept safe.
- Connectivity: 5G uses millimeter wave spectrum and offers unprecedented speed, low latency, and bandwidth capacity, that enables manufacturers to do more with the mega expansion of the Internet of Things (IoT), as well as collect more data, and compute more information faster to make better business decisions. Accenture predicts that 5G tech “will create a more seismic impact than any wireless technology evolution to come.”
- Scalability: Choose a solution that can grow and evolve with your business over time, so that you don’t have to keep replacing your automation technology every few years.
- Ease of use: Choose a solution that is user-friendly and easy for your staff to learn and operate. This will minimize any disruption to your existing processes and help you to get the most out of your automation technology from day one.
- Alignment with business outcomes: Ensure any automation solution you choose is aligned with your business goals and objectives. This means understanding what you hope to achieve through automation, whether that’s reducing labor costs, improving production efficiency, or enhancing quality control.
How humans and machines can help each other
I am a firm believer that growth thrives at the intersection of tech and humanity. By embracing industrial automation, manufacturers can improve their overall efficiency, reduce the risk of errors, and increase their output capacity, leading to higher profitability and a competitive edge in the market.
As the global industrial automation market grows, it’s becoming clear that humans and machines can work together to achieve greater business results. However, we must address potential concerns around job displacement and ensure that automation complements human skills and creates new opportunities for the workforce.
To fully realize the benefits of industrial automation, we need to prioritize humans as well. This means designing automation systems that are intuitive and easy to use for humans, incorporating human-centered design principles into the development of automation technology, and investing in training programs to help workers develop the skills needed to succeed in a world where machines play an increasingly important role.
When we embrace the power of collaboration between humans and machines, we open up endless possibilities for unlocking new levels of productivity, creativity, and innovation. This exciting partnership paves the way for a brighter future, where humans and machines can work side by side in harmony, bringing forth ideas and solutions that were once impossible. Let’s embrace this incredible opportunity to harness the full potential of our technology advancement and inspire more autonomous, innovative, connected, and resilient manufacturing.
Learn about AT&T Business manufacturing solutions or contact your AT&T Business representative.
1Laura Ross, “The outlook of automation in 2023.” Thomasnet.com, March 20, 2023, https://www.thomasnet.com/insights/the-outlook-of-automation-in-2023/
2“Retail automation market to surge USD 34.23 billion by 2029, share, size, emerging trends, key growth drivers. Challenges, and segments,” PRNewwire.com, Nov 02, 2022, https://www.prnewswire.com/news-releases/retail-automation-market-to-surge-usd-34-23-billion-by-2029--share-size-emerging-trends-key-growth-drivers-challenges-and-segments-301666303.html
Share
Share this with others