An AI-human driven world in the manufacturing industry
This post was sponsored by AT&T Business, but the opinions are my own and don’t necessarily represent AT&T Business’s positions or strategies.
Artificial intelligence (AI) manufacturing is a long way from anything early manufacturers could have imagined. Through machine learning, software is able to intake and process information and analyze data to make faster, smarter decisions. Early engineers would revel at the idea of finding a problem before it caused painful dollars in scrap. And today, manufacturers are able to learn, innovate, and create at a pace that was once only fiction.
It’s clear that manufacturing has come a long way since Henry Ford’s revolutionary creation of the assembly line in 1913. He launched us toward a world where machines and humans work side-by-side. Ford would be amazed by how far manufacturing processes have come and likely floored by AI in manufacturing where human-machine collaboration operates in a new way—a way that drives innovation forward at an unprecedented speed. Today’s factories are agile and full of power and possibilities. They’re full of industrial Internet of Things (IoT) sensors, which helps create a neural network that mimics the intelligence of the human brain. They’re smart.
Industrial IoT is just one component of the new factory, defined as Industry 4.0. Artificial Intelligence (AI) in manufacturing is defining the new smart factory—Industry 5.0. Real-time data through industrial IoT is combined with a principal element of AI: machine learning, that is, teaching machines to recognize patterns and make determinations. Now, intelligent machine-to-machine communication and predictive maintenance are driving better decision making, reliability, and outcomes, such as faster data-informed innovation and lower overhead for manufacturers.
Digital revolution has made a massive impact on manufacturers from a collaboration, collection of data, and command and control perspective. What I am most excited about, however, is the convergence aspect of this story—seamless systems working together in the best way possible to maximize capacity, maximize control, and maximize time horizon from a network perspective, as well as a people, process, and technology perspective.
In the next 10 to 20 years, connected manufacturers will be smarter, more autonomous, and more sustainable with less waste and less downtime. They’ll be able to produce more with the same resources and adjust faster to market demands and conditions. Kudos to innovators and enablers like AT&T Business who, in particular, are connecting the world with 5G and reimagining data at the edge. The factory of the future is not something to be feared, but a vision to be embraced and a modern stepping stone to reaching our greatest potential.
Here, we explore the evolving role of AI in manufacturing and the vast potential of AI and human collaboration.
IoT and connectivity is the common page for people and machines
When I think about the digital revolution, AT&T plays a vital role in providing the technology and connectivity that enables people to do more.
The future of manufacturing is autonomous and sustainable. A 5G network ensures bandwidth, speed, and low latency needed for the data-driven demands of manufacturing.
One of the biggest challenges we face today is a labor shortage. The U.S. Chamber of Commerce reports the manufacturing industry lost approximately 1.4 million jobs during the beginning of the pandemic. As of August 2023, it still had a total of 616,000 jobs left unfilled.”1
How will we fill these positions? Here’s how I see it:
- Automate so that people augment manufacturing, not by replacing humans with technology.
- Use AI to help people with disabilities perform jobs they couldn’t do otherwise. Give them a life-changing opportunity to be independent and fill the labor shortage gap.
- Improve worker safety with monitoring systems that send alerts automatically to management.
- Use predictive maintenance to determine the deterioration of machines and save unnecessary costs and downtime.
Moving toward collaboration between humans and AI technologies
I have long believed that growth thrives at the intersection of tech and humanity. The shift towards collaboration between human workers and AI technologies is underway, not because AI is the latest technology out there, but because AI is enhancing what manufacturing has always done well: making products to better our lives. In a recent interview, I discussed key areas where the smart factory is making an impact:
- Improving operational uptime and productivity with sensor technology
- Extending the life expectancy of fixed assets with smart maintenance versus a predetermined schedule
- Saving money on maintenance, replacement, and waste
- Improving worker health and safety
AT&T Business is creating the path to smart factory solutions with AI-enabled technology and connecting the factory so IoT devices deliver the data manufacturers need to make better decisions. They provide a secure, reliable network that ensures you can automate and build a connected, sustainable, smart manufacturing business.
The complementary relationships between AI and humans
According to Beth Stackpole in the MIT Sloan Management Review, step one for AI manufacturing is data. Yet, for many midsize manufacturers, data modeling has not been an easy task. “Manufacturing data is often localized or specific,” Stackpole states, “to a particular industry domain or a company’s operations. As a result, there isn’t a lot of relevant data available for building reliable AI models …”2
And there’s no universal language as one would expect in the financial, retail, or other sectors. Stackpole suggests a “data-centric vertical AI platform, which can facilitate specific use cases. For example, an automated anomaly detection tool could replace or augment human workers who are tasked with quality control.” In other words, let the data drive the AI training rather than algorithms.
A final salient thought from the article is to use generative AI to close the gap between workers who are not coders, but who could use human speech to communicate with a system.
Boston Consulting Group (BCG) points out that lean manufacturing is no longer enough and that data, advanced analytics and AI-powered tools “across the entire manufacturing value chain” is key to actionable insights on the shop floor.
According to a BCG survey, conducted in 2023, one in six manufacturers have met their AI-related objectives to date. BCG explains the gap is due to “inadequate organizational and technological foundations, which are essential for scaling AI solutions throughout production networks.” Like MIT Sloan Management Review, BCG talks about generative AI as a pathway to reimagining operations. It cites the example of giving workers “detailed work instructions, including visualizations and the required spare parts, for specific maintenance incidents.”3
The workplace has changed dramatically since 2000 with AI further evolving careers. One of the most exciting advances is integrating AI in the hiring of people with disabilities. To me, this is the ultimate example of how humans and AI can work together.
I’ve written about just such a collaboration. Clover Imaging Group is the largest collector and re-manufacturer of printer cartridges in the world. Clover used Microsoft’s Azure technology to empower warehousing employees with cognitive disabilities through conversational AI and a mixed-reality platform.
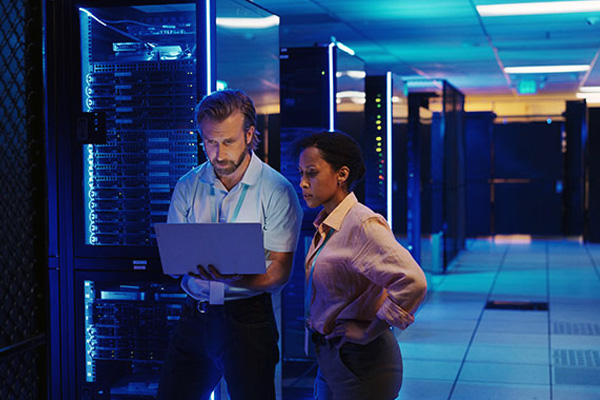
Using AI to drive business success
Using AI can be a game changer for scaling your business. Andy Markus, CDO from AT&T Business, discusses using AI for smarter business decisions.
Key applications evolving in AI manufacturing
How are manufacturing companies using AI today?
I found a plethora of examples in an article by financial and investment publisher The Motley Fool. It cites five areas where manufacturers are deploying AI: robotics, quality, predictive maintenance, robotic process automation (RPA) for repetitive tasks, and supply chain. Here’s a quick hit list of companies using AI in the manufacturing world.
- Ford uses robots to operate 3D printers autonomously at night, spewing out 3D designs previously uploaded to the printer by a human being.
- Samsung, Google, and NVIDIA utilize machine learning for “quality control, optimizing chip design and making manufacturing improvements.”
- Washington, D.C., uses predictive maintenance technology from IBM to maintain water hydrants.
- Whirlpool uses Robotic Process Automation (RPA) to automate its assembly line and handle materials. Quality control checks are done by bots.
- BMW uses AI to predict demand and optimize inventory.4
AI-driven robotics and automation have revolutionized manufacturing processes. Robots equipped with AI can carry out repetitive tasks with precision and speed, leading to increased production rates and improved product quality. AI amplify the value of predictive maintenance and supply chain management.
Getting started with AI-enabled technologies in manufacturing
Nothing is more challenging than the blank page. Manufacturing has historically been a slow adopter to new technologies. So where do makers start when it comes to deploying AI-enabled technologies?
First, explore AI-enabled solutions to stay competitive. I recommend anyone who is working in a factory to visit robots on the plant floor, learn how they operate and interact with humans. Visit the AT&T Business exhibit at MxD in Chicago and explore. Learn how the digital revolution is transforming business and what a smart factory really looks like.
Second, remove the fear (I would call it a myth) of being replaced by AI and encourage team members to learn more about AI. Pique their interest with lunch-and-learns or guest speakers. By taking a leap of faith to embrace automation in manufacturing, you’re ushering in a whole new world of opportunities to reimagine what happens on the production floor and the bottom line.
Third, if you’re a new graduate, don’t limit yourself to sitting in the corporate office. Go to companies that make things. You can find a job in an office later. Hands-on experience for the younger generation demonstrates the value of being a creator. Make something before you manage people. I worked for a refinery and then a tractor company. Those experiences gave me great exposure to how things were made. When I became a financial forecaster, I could imagine my work’s impact on the day-to-day operations of those who made things. Those experiences were valuable.
Fourth, adopt a future mindset, thinking beyond what is happening right this moment. What can be done tomorrow that isn’t being done today? Dare to innovate. Having the right people around you will equip you with confidence. AT&T Business has an entire professional services team to guide you with your IoT vision and execution.
AI manufacturing is human driven
The future of manufacturing is bright, driven by the powerful collaboration between humans and AI. At its most basic level, AI-human collaboration in the manufacturing industry is important because it draws on the strength of both people and machines and opens a world of opportunities. Just as it always has. Just as Henry Ford understood when he invented the innovation of the assembly line. AI manufacturing brings out the best of both makers and machines.
We've explored the remarkable potential of AI-human collaboration in the manufacturing industry, highlighting the ways in which it enhances productivity, safety, and innovation. The evolution of smart factories is not something to fear but to embrace as we step into a future where machines and makers work together.
As we move forward, remember that the United States has always been a nation of doers, of creators, of makers. The same spirit that drove Henry Ford to transform manufacturing is alive today, only now we have the tools of artificial intelligence to magnify our capabilities. The solution to our challenges lies in the seamless partnership between humans and machines, working together to drive progress and excellence. Manufacturing can go all the way with AI manufacturing. But you must have the guts to invest, hire people with the right skill sets, and adopt an innovation mindset to build the infrastructure and reimagine the possibilities of how you make products in the future.
Thank you for joining me on this journey to explore the expanding role of IoT and connectivity, the collaboration of humans and AI, how they complement one another, key applications where companies today are using AI in manufacturing and steps you can take to start integrating AI into your factory. The evolution of smart factories is not something to fear but to embrace as we step into a future where machines and makers work together.
Now, it's your turn to take the next step and be a part of this transformative journey.
Why AT&T Business?
See how ultra-fast, reliable fiber and 5G connectivity protected by built-in security give you a new level of confidence in the possibilities of your network. Let our experts work with you to solve your challenges and accelerate outcomes. Your business deserves the AT&T Business difference—a new standard for networking.
Learn more about AT&T 5G solutions for business and AT&T Internet of Things. To connect with an expert who knows business, contact your AT&T Business Representative.
1“Understanding America’s Labor Shortage: The Most Impacted Industries,” U.S. Chamber of Commerce, Accessed January 11, 2024, https://www.uschamber.com/workforce/understanding-americas-labor-shortage-the-most-impacted-industries.
2Beth Stackpole, “For AI in Manufacturing, Start with Data,” MIT Sloan, June 28, 2023, https://mitsloan.mit.edu/ideas-made-to-matter/ai-manufacturing-start-data.
3“MFG AI’s Integrated Offering for AI-Powered Manufacturing,” BCG Global, Accessed November 3, 2023, https://www.bcg.com/videos/mfg-ai-integrated-offering-for-ai-powered-manufacturing.
4Jeremy Bowman, “5 Examples of AI Uses in Manufacturing,” The Motley Fool, Accessed November 3, 2023, https://www.fool.com/investing/stock-market/market-sectors/information-technology/ai-stocks/ai-in-manufacturing/.