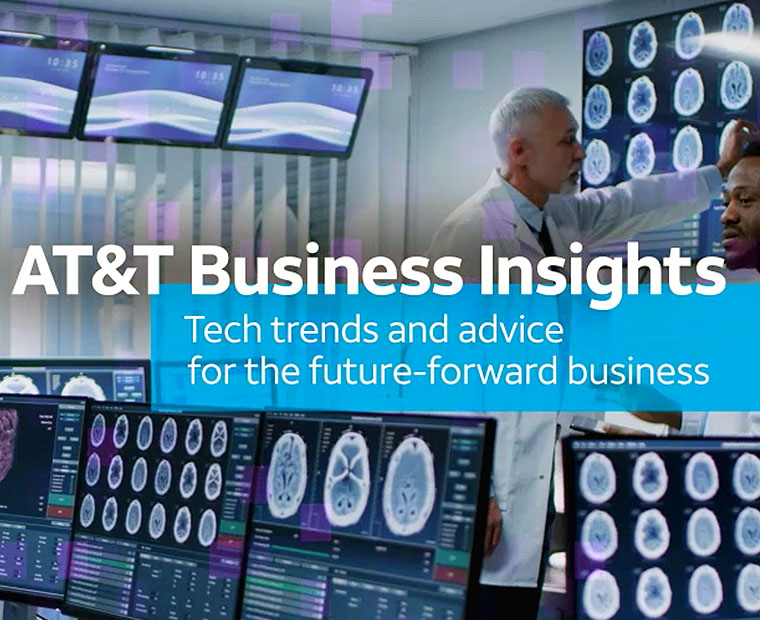
Featuring: Internet connections
Staying connected: Understanding your internet connections
by: Zoya Cochran, Managing Editor, AT&T
10 min read
Your internet connectivity options vary by location, usage, and internet backup plans. Learn when fiber, 5G, or other solutions may best support your business.
10 min read
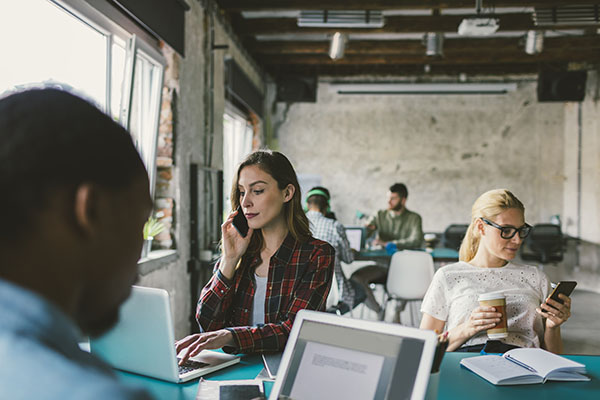
In this Article
- How data moves across a network
- Types of internet connections
- How Wi-Fi works with your internet connections
- Choosing the right internet connection to optimize your business
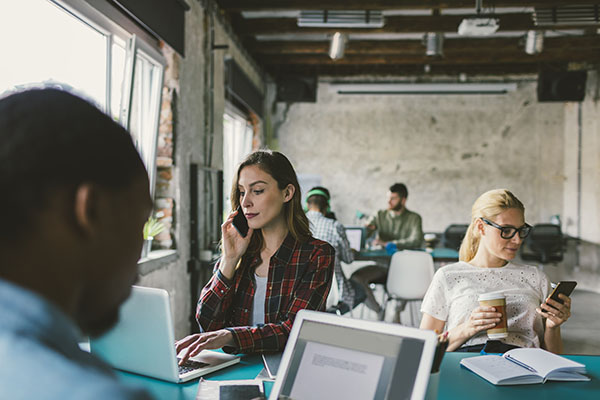
Latest articles
Search Result:
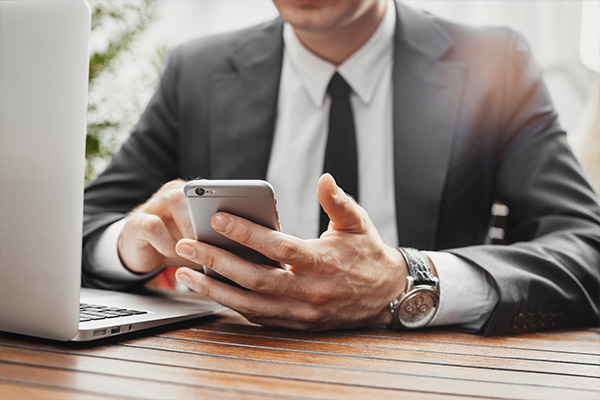
Read what AT&T Office At Hand and other unified communications as a service can do for your future-ready business.
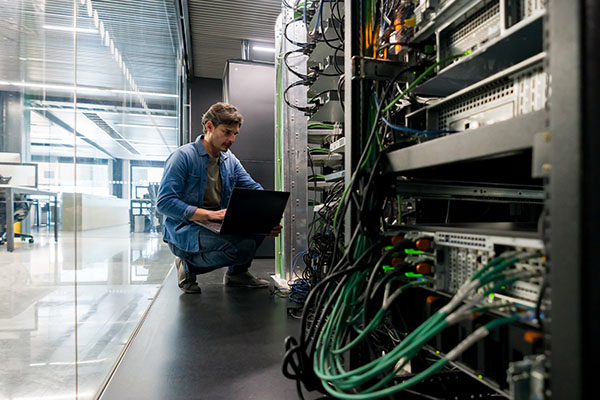
Many organizations still use outdated systems that slow down productivity, increase security risks, and limit growth. It’s time for network modernization.
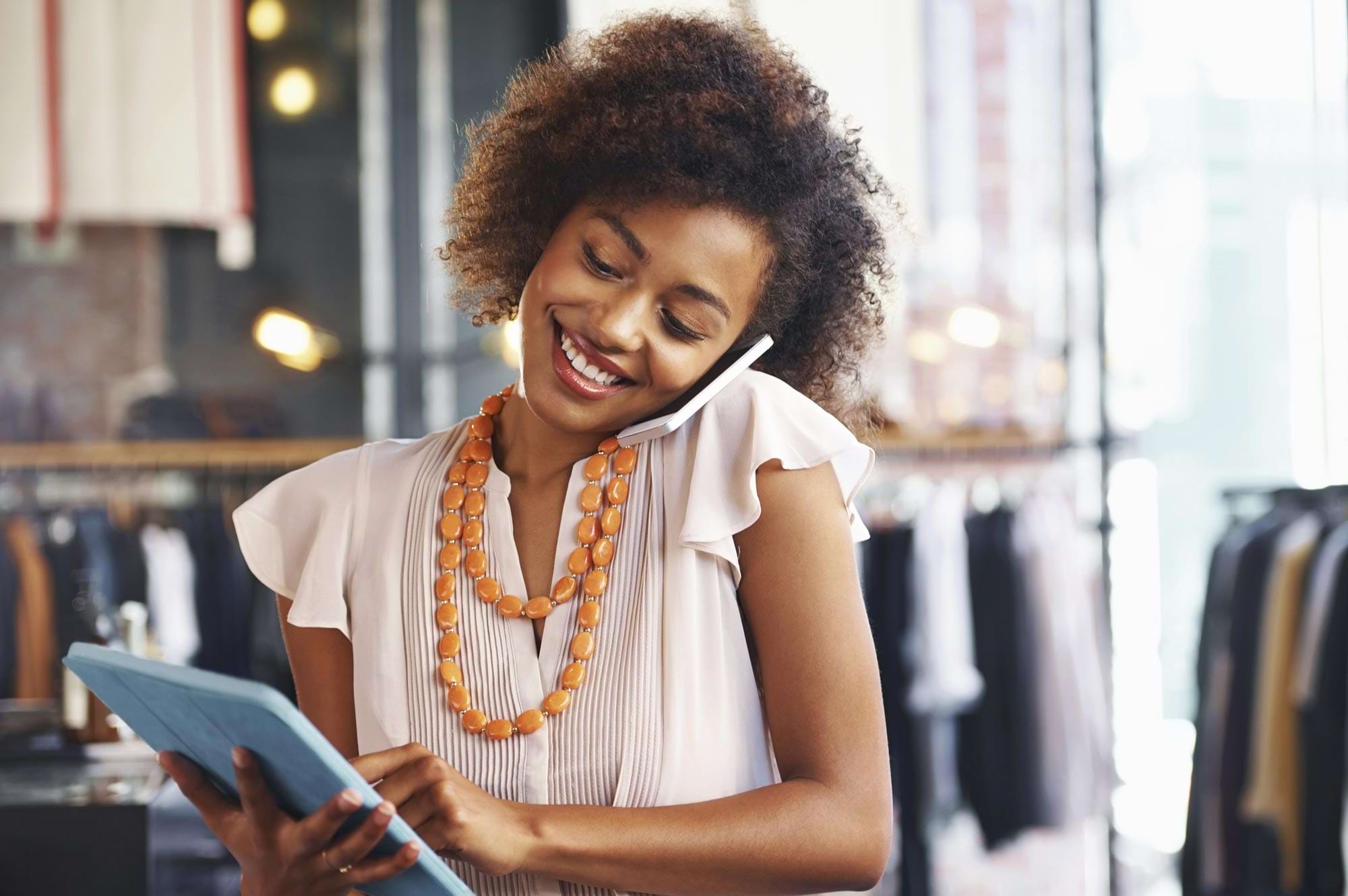
Learn the basics of voice over IP (VOIP) technology that enables you to make phone calls anytime, anywhere using an internet connected computer and a headset.
Filter By
INDUSTRY
- All industries...
PRODUCT CATEGORY
- All products...
TYPE
Never miss an update on the latest tech trends for business
Subscribe today!
By submitting your email address, you agree to receive future emails from AT&T and its family of companies.
We’ll email you offers and promotions about AT&T products and services.
By submitting your email address, you agree to receive future emails from AT&T and its family of companies.
We’ll email you offers and promotions about AT&T products and services.
- Terms of use
- Your privacy center
- Accessibility
- Your Privacy Choices
- Health Privacy Notice
- Cyber Security
© AT&T Intellectual Property. All rights reserved. AT&T, the AT&T logo and all other AT&T marks contained herein are trademarks of AT&T intellectual property and/or AT&T affiliated companies. All other marks are the property of their respective owners.