The digital factory in manufacturing: Automation
Automating a factory can save money, improve safety, and standardize product output and quality
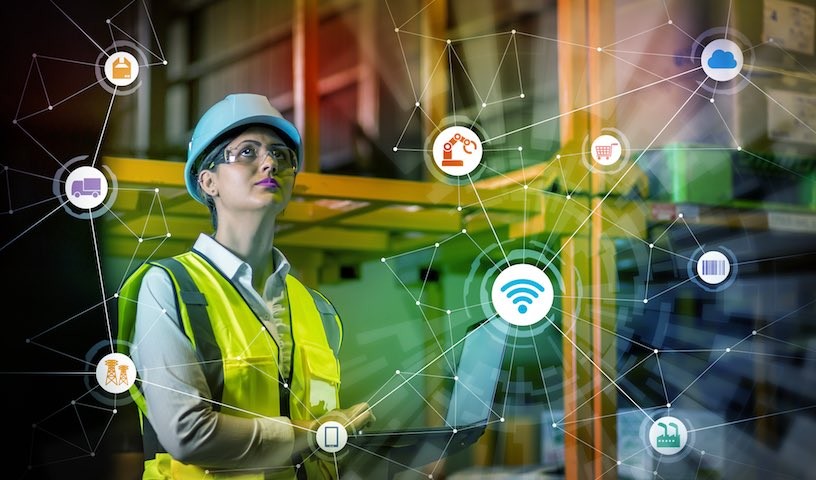
This post is the third in a three-part series that examines elements of the digital factory.
Automation is a goal for virtually every manufacturer and has been for years. Automating a factory floor can save money, improve safety, and standardize product output and quality.
According to TheManufacturer.com:
“Manufacturers’ production lines often are not optimally efficient primarily due to the inability of humans to monitor and react to every small change during the manufacturing process. This monitoring itself can now be automated in connected factories through the use of IoT devices, which can autonomously decide to take action or call for specialized human help,”
This example demonstrates the intersection of digital transformation and automation, which is changing the face of the factory forever.
Pairing automation with technology creates so-called smart factories, which are poised to add between $500 billion to $1.5 trillion in value to the global economy over the next five years, according to Capgemini. This may be why 76% of manufacturers have or plan smart-factory initiatives. It’s clear: Automation is so important that companies are doing whatever it takes to make it happen.
This is not a task to undertake without careful thought and planning, though, according to Greg Nichols of ZDNet.com. “The problem is that adding automation post hoc to industrial operations is difficult and pricey. Deployment has typically required weeks, in addition to a lot of upfront capital,” he writes.
Cumulatively, smart factories will drive higher productivity at a lower cost base, strengthening manufacturing P&L in the short term and improving firms’ competitiveness in the long runShare this quote
To succeed, companies must think big, according to a recent report by Deloitte Insights:
“Starting small with manageable components, and scaling quickly to grow the operations, the promise and benefits of the smart factory can be realized … Manufacturers that want to win in tomorrow’s increasingly connected and disrupted environment will need to move from being organizations with a smart manufacturing capability to become digital enterprises.”
“Small programs, known as lighthouse projects” help manufacturers test digital initiatives and act as proof-of-concept programs, says Boston Consulting Group (BCG). It’s not enough to simply automate an assembly line, however. Manufacturers also must consider the types of technologies to align with automation.
A recent study by Capgemini found that “digital masters” – those who are at an advanced stage in digitizing production processes and have strong vision and skills – use tools such as big data and advanced robotics to help with automation on the factory floor.
Digital masters also concentrate on training and governance, making sure employees are skilled and knowledgeable when it comes to data analytics, automation, and cybersecurity. Finally, they set aggressive targets and focus “on the financial impact of an end-to-end manufacturing transformation rather than technological improvements.”
Pairing automation with technology creates so-called smart factories, which are poised to add between $500 billion to $1.5 trillion in value to the global economy over the next five yearsShare this quote
While creating a factory of the future – one that incorporates automation and other technologies – won’t be easy, it is certainly worth the work. Capgemini’s recent study explains it best: “Cumulatively, smart factories will drive higher productivity at a lower cost base, strengthening manufacturing P&L in the short term and improving firms’ competitiveness in the long run.” But by how much? According to BCG: “In our experience, a best-in-class productivity program can generate a 3- to 6-percentage-point increase in earnings before interest and taxes (EBIT).” Not a bad goal for anyone.
Learn to grow your business with industry-specific solutions and IoT Manufacturing.
Share
Share this with others